500 mesh iron powder

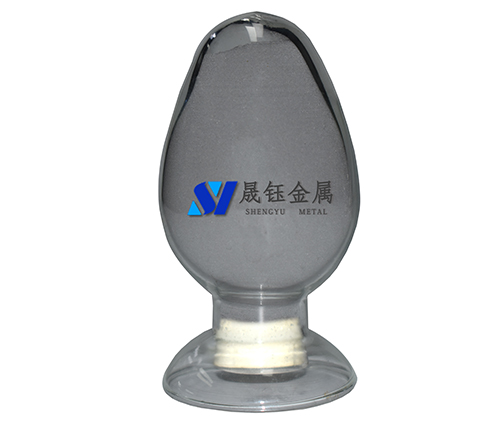

Commodity details
Reasonable particle size distribution and beautiful particle shape;
High compressibility, can reach 7.20g / cm3;
Excellent sintering performance;
High sintering strength;
The process of making metal powder by water atomization has a long history. In ancient times, people poured molten molten iron into the water, causing it to burst into fine metal particles, which were used as raw materials for making steel. Water atomized pure iron powder. Until now, there are still people in the folk who pour molten lead directly Make a lead shot into the water. The water atomization method is used to make coarse alloy powder. The process principle is the same as that mentioned above for water to burst metal liquid, but it has greatly improved the crushing efficiency.
The high-pressure water atomization method is used to make coarse alloy powder. The crude gold is first melted in a furnace. The molten gold solution must be overheated by about fifty degrees, and then injected into the tundish. Start the high-pressure water pump before the gold liquid is injected, and let the high-pressure water atomization device start the workpiece. The gold liquid in the tundish passes through the beam and enters the atomizer through the leakage nozzle at the bottom of the bag. The atomizer is the key equipment for making coarse gold alloy powder by high-pressure water mist. The quality of the atomizer is related to the crushing efficiency of the metal powder. Under the action of the high-pressure water from the atomizer, the gold liquid is continuously broken into fine droplets, which falls into the cooling liquid in the device, and the quick liquid solidifies into alloy powder. In the traditional high-pressure water atomization process for making metal powder, metal powder can be continuously collected, but a small amount of metal powder is lost with the atomized water. In the process of making alloy powder by high-pressure water atomization method, the atomized product is concentrated in the atomization device, and is precipitated and filtered. Alloy powder, there is no loss of alloy powder in the whole process.
Atomization method, general characteristics: powder particles are close to spherical, high bulk density, good fluidity, and high compaction strength. Main uses: high-density structural parts, powder forged parts, filters, welding rods. The price is more expensive.
Iron dust An aggregate of particles of iron with a size of less than 1 mm. Colour: Black. Is the main raw material for powder metallurgy. According to the particle size, it is customarily divided into five grades of coarse powder, medium powder, fine powder, fine powder and ultrafine powder. Iron powder with a particle size in the range of 150 to 500 μm is coarse powder, particle size is 44 to 150 μm is medium powder, 10 to 44 μm is fine powder, 0.5 to 10 μm is extremely fine powder, and less than 0.5 μm is ultra fine powder.
Generally, the powder that can pass through a 325 mesh standard sieve, that is, the particle size is less than 44 μm, is called sub-sieve powder. For more high-precision screening, only air classification equipment can be used. Do it with a nitrogen protective classifier. Iron powder mainly includes reduced iron powder and atomized iron powder, which are named because of different production methods.